Nagami 3D-prints plastic to mimic melting glaciers in Spanish boutique
Spanish design studio Nagami completed a shop interior for the sustainable clothing brand Ecoalf near Madrid from recycled plastic.
Walls, shelves, and display tables inside the store in the Las Rozas Village designer outlet are made from 3.3 tonnes of repurposed plastic waste, sourced mainly from hospitals and used to create translucent surfaces that resemble melting glaciers.
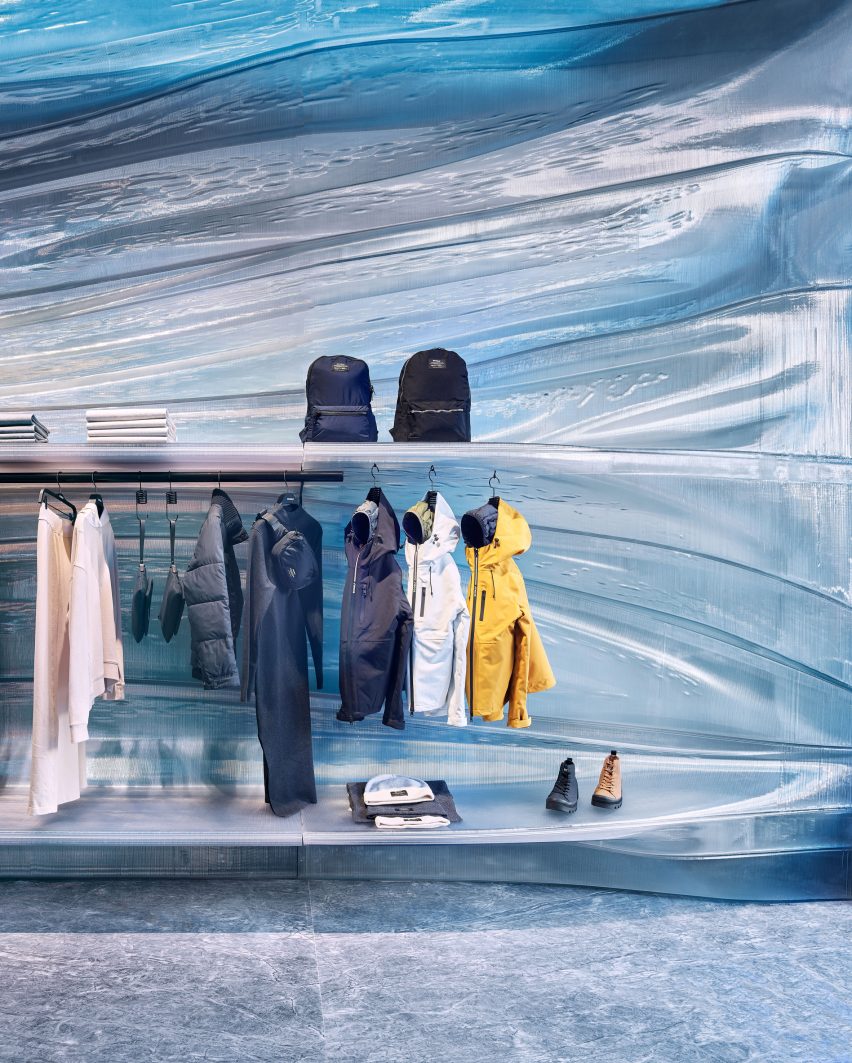
Additionally, Additive manufacturing specialist Nagami created the plastic panels using a robotic arm equipped with a custom-built extruder that can print complex 3D forms, to unite design and technology to raise awareness about the climate crisis.
“We wanted to highlight the melting of the polar glaciers due to climate change,” Nagami co-founder Manuel Jiménez García told Dezeen. “So the walls are meant to represent a glacier that is cracking.”
“The 3D-sculpted texture is a reference to the way the wind and snow erode the ice over time,” he added. “The idea was to recreate the sensation you might have when walking inside a glacier.”

Additionally, The Ecoalf store is the first fully 3D-printed interior completed by Nagami. And García believes it may be the first in the world to be fully 3D-printed using recycled plastic.
Moreover, The project was completed with a very short lead time of just three months from design to installation.

Moreover, According to García, the undulating forms that cover almost all of the store’s internal surfaces pushed the robotic printing technology to its limit.
“The machines needed to dance to create all of these different angles,” the designer explained. “Traditional 3D printing uses layers. But we can change the angle of the robot to make the kinds of curved and wavy forms you see in this project.”
The walls are into panels and joined using connectors that form part of the printed structure. This meant that the tolerances needed to be very precise so that the components can slot together neatly.
On the floor, natural stone tiles feature veins reminiscent of cracking ice to enhance the feeling of walking on a glacier.
Moreover, All of the components used for the interior can be disassembled and reused or recycled for future projects. The plastic itself is almost infinitely recyclable, losing just one percent of its structural performance with each new use, Nagami claims.

Both companies share an interest in sustainable manufacturing, with Ecoalf creating clothing, footwear, and accessories using recycled materials including plastic bottles, discarded fishing nets, used tires, and post-industrial wool and cotton.
Similarly, Nagami works with recycled plastic to create furniture, sculptures, interiors, and architectural elements as part of a closed-loop production process.
The studio’s previous projects include several window displays for Dior, as well as a mobile toilet cubicle called The Throne. And a collection of 3D-printed chairs by designers including Ross Lovegrove and Zaha Hadid Architects.

During the coronavirus pandemic, Nagami made use of its quick-fire production process to 3D print face shields for medical staff.
“We see 3D printing as one of the most sustainable forms of production,” García explained. “You don’t have to produce stock, it doesn’t create any fumes and it’s very versatile. So you can create things on demand.”
“In the future as we expand we want to have production sites around the world making things locally. And reducing our carbon footprint even further.”
Finally, read more on Archup: